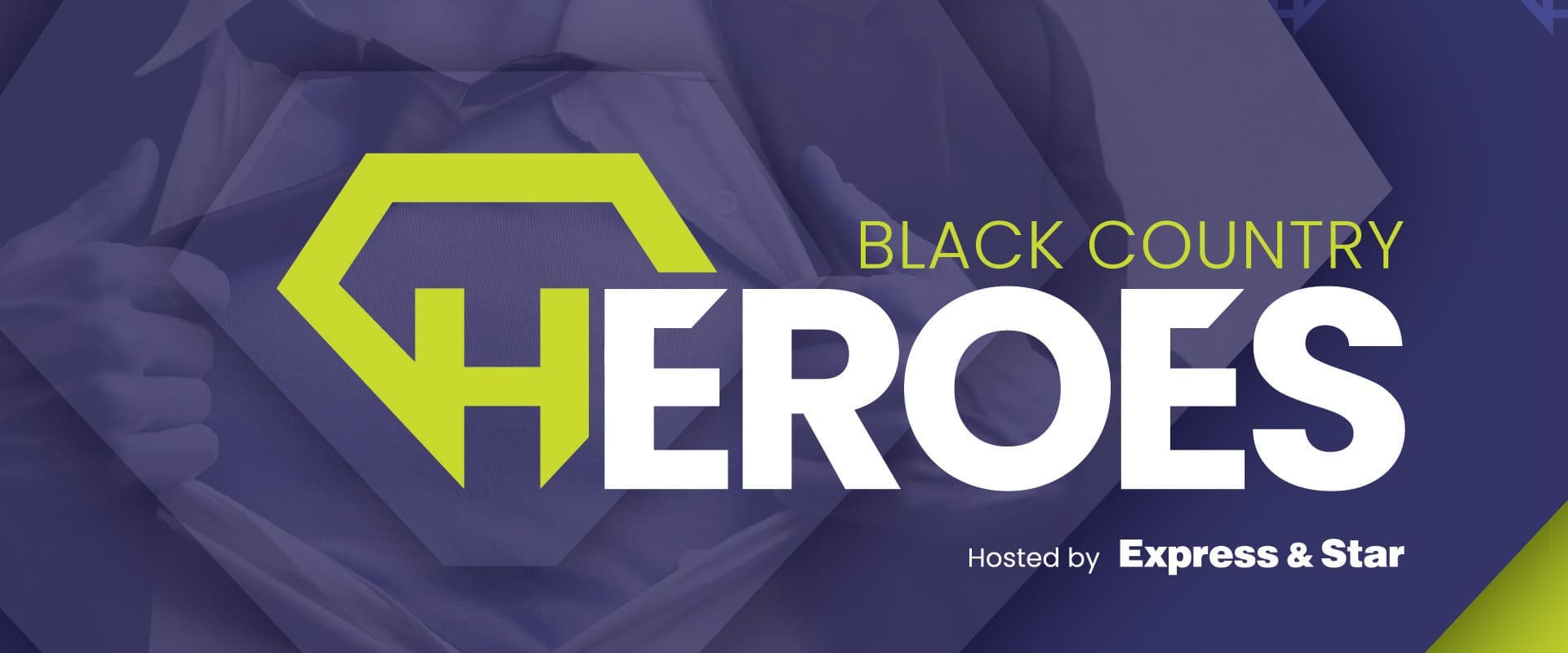
Building the Future, Celebrating Our Youth: Varlowe Sponsors Black Country Heroes
We are proud to announce our sponsorship of the Black Country Heroes initiative. This inspiring program recognises the remarkable individuals who make this region a vibrant and thriving place. We’re particularly excited to support the Future Stars category, which shines a light on the exceptional young people shaping the Black Country’s future.
Why We Support Black Country Heroes
At Varlowe, we believe in the power of community. We’ve been rooted in Wolverhampton for over two decades, serving clients across the UK with our expertise in CNC machining, steel fabrication, specialist pipework solutions, and more. But beyond engineering excellence, we’re passionate about giving back and investing in the future of the Black Country.
The Black Country Heroes program perfectly aligns with our values. It celebrates the individuals who embody the region’s spirit of hard work, dedication, and a commitment to excellence. These are the very qualities that drive our team at Varlowe.
What is the Black Country Heroes Future Stars Category?
The Black Country Heroes Future Stars category recognises extraordinary young people aged 21 or under who have demonstrated significant progress and growth in the past year. These young heroes can excel in various fields, from academic achievements and sporting prowess to entrepreneurial ventures and personal development journeys.
The program acknowledges their potential and celebrates their contributions to the Black Country. By highlighting these inspiring individuals, it encourages others to pursue their dreams and make a positive impact on their communities.
More information about the category can be found on the Black Country Heroes website.
Why We Champion Young Talent
As a family-run business, we understand the importance of nurturing young talent. The young people of today are the engineers, innovators, and leaders of tomorrow. They are the ones who will shape our communities, drive progress, and build a brighter future.
By sponsoring Black Country Heroes Future Stars, we aim to:
- Recognise and celebrate exceptional young people: Their achievements and dedication deserve recognition, and we believe it’s crucial to showcase their stories as an inspiration to others.
- Encourage young people to pursue their dreams: We want to send a message to young people in the Black Country that anything is possible with hard work and dedication. Black Country Heroes provides a platform to showcase their talent and motivates them to reach their full potential.
- Invest in the future of the Black Country: By supporting young talent, we invest in the long-term success and dynamism of the region. These young heroes are the future workforce, entrepreneurs, and community leaders who will shape the Black Country’s path forward.
Spotlight Varlowe’s Youth Initiatives
Our commitment to young talent goes beyond the sponsorship of Black Country Heroes. We are proud to have an apprentice in our CNC machine shop, actively investing in developing future engineering professionals. Additionally, we’ve been strong supporters of local up-and-coming athletes and associations, such as boxers and local football teams. We believe in empowering young people to reach their full potential, both within the engineering field and in their chosen passions.
How You Can Get Involved
The Black Country Heroes initiative thrives on community participation. Here are ways you can get involved and celebrate the region’s exceptional individuals:
- Nominate a Future Star: Do you know a young person who exemplifies the Black Country spirit and deserves recognition? Nominate them for the Future Stars category! Visit the Black Country Heroes website for more information and nomination details.
- Spread the Word: Share the Black Country Heroes program with your networks and encourage others to nominate deserving young people.
Building the Future Together
Varlowe Industrial Services is proud to participate in the Black Country Heroes initiative. We are committed to supporting the region’s future by championing its most valuable asset—its young talent. By working together, we can empower young people, celebrate their achievements, and build a brighter future for the Black Country.
If you know someone who deserves the award, please use the following link to nominate them: https://blackcountryheroes.expressandstar.com/.