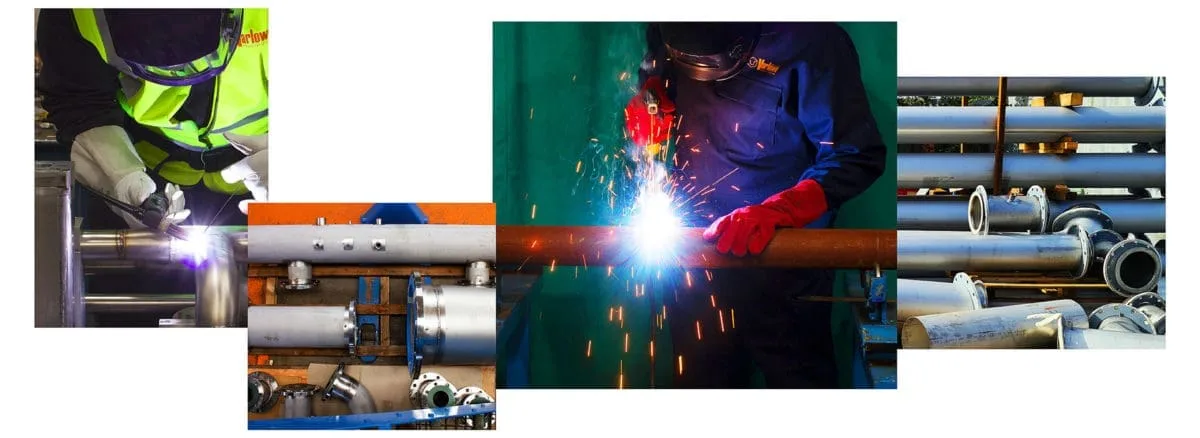
A Mechanical Contractor manages the mechanical projects for many different companies. They are skilled professionals who can keep essential mechanical systems running optimally.
Serving in nearly every industry, they have a wide range of expertise across all trades.
Generally, a mechanical contractor is in charge of the following:
- Plumbing
- Refrigeration
- HVAC
- Electrical Systems
- Pipework Fabrication
- Ductwork
- Gas Work
They problem-solve to find the faults that cause a system to fail. Then they will provide vital fixes by careful and calculated changes.
Part of the problem solving is taking into account the practical installation. They have to monitor a system’s costs and energy efficiency closely.
Some contractors will work on a project during inception and installation. Others will be involved and manage the ongoing maintenance and repair.

Duties of a Mechanical Contractor
A mechanical contractor is a jack-of-all-trades. They can work on a variety of different projects in many other trades. As long as there are mechanical parts, they ensure that everything is installed and working correctly.
Typically, their duties involve organising with other trades to complete the project. Any delays can cause a knock-on effect and impact the completion of a project. Therefore, Coordination between trades is vital as they work to strict time and budget scales.
Mechanical contractors will often design and manufacture parts ahead of time. Because of this, they are saving time and any disruption on site.
The other primary duty of a contracting company is to carry out maintenance on existing systems.
A regular maintenance process keeps all parts of these complex mechanical systems are in good working order. They allow you to continue your work without suffering losses from downtime.
Even though issues can still occur even under regular maintenance, most are addressed in a few hours.
In other words, regular maintenance reduces the likelihood of catastrophic problems that can cripple a business.
Varlowe’s Contracting Services
Varlowe is a mechanical contractor specialising in high-pressure pipework systems. We have been effective for making real benefits through careful planning.
The team of trained engineers can provide practical solutions on site. Our contract managers offer the knowledge to see you through the project. Above all, from start to finish, you will receive a high-quality service.
For more information on our services, please visit our services page.
Give us a call on 01902 861042 to chat with one of our team. You can also email info@varlowe.co.uk or visit our contact page to fill out a form.