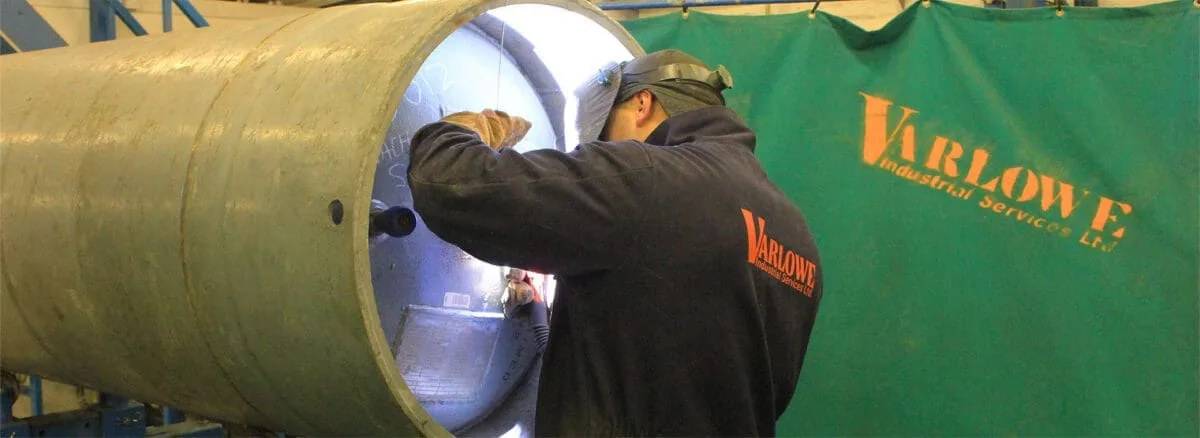
What Is A Coded Welder?
To put it simply, a coded welder is someone who has completed a Welder Approval Test in a specific welding configuration.
The welding code system is created to demonstrate a welder has the knowledge and skills to carry out work to industry standard requirements.
Some codes can vary, but most of the time, they are particular and need individual parameters allocated via a weld test inspector.
Welder Coding
Codes manage and regulate the various welding processes and procedures that exist.
In the U.K., welder approval codes are to BS EN ISO standards. The USA uses the ASME IX and AWS standards.
A welding specification requires testing to that specification. The welder will offer a welding sample that mirrors the position as closely as possible.
You will produce a weld following written instructions. An approved CSWIP examiner will then perform a:
- Visual Or Surface Inspection
- Destructive Bend Test
- Nick Break Fracture Test
- Macro Etch
Approval tests examine a welder’s skill and ability under pressure.
Testing demonstrates that a welding procedures design is fit for purpose, producing a welded joint that will meet the mechanical and quality requirements for the job. If the welder passes, they are Coded to that specification.
Being Coded in a particular specification does not mean you are qualified in another, even though you are Coded.
Each specification requires training, tests and examination, becoming a multi-coded welder.
As a coded welder, you will possess the skills required to work in some of the most highly regulated sectors. You will work on various safety-critical applications, such as vessels and high-pressure pipework.
BS EN ISO 9606, ASME Section IX are appropriate for welders working on pressure vessels, piping, off-shore structures and for other products where the consequences of failure are catastrophic such as structural steel.
How Long Do Welding Codings Last?
For qualifications to remain valid, certificates must be signed by either their employer/welding coordinator or an examiner every six months. ISO 9606 requires welders to retest every three years.
List Of Codes For Welding
The goal of welding codes is to facilitate a safe work environment and enforce proper procedures by improving welder skills and processes.
Some unique coding systems come from the International Organization for Standardization (ISO) and the American Welding Society (AWS).
The AWS issues over 240 codes, recommended methods and principles written under the American National Standards Institute practices (The American National Standards Institute (ANSI) administers and coordinates the U.S. voluntary standards and conformity assessment system).
The International Organization For Standardisation is an organisation that consists of various national standards bodies. As of 2022, there are 167 members representing ISO in their country.
Other know standards are the American Society of Mechanical Engineers (ASME), British Standards (B.S.) and Canadian Standards Association (CSA).
For a complete list of Welding Codes, follow this link – Https://en.wikipedia.org/wiki/List_of_welding_codes.
Common Welding Codes
In welding, documents known as codes set a standard of practice that ensures quality is maintained throughout.
Developed by a mixture of associations, Welding codes set the conditions for:
- Inspection
- Testing
- Repair
- Approved Materials
- Fabrication
- Design Specifications
- Welding
As a coded welder in the U.K., you will be operating under one of the following:
- B.S. – National British Standard
- BS EN – European British Standard European Standard
- AWS – U.S. American Welding Society
- ASME – American Society of Mechanical Engineers
- ISO – International Standards Organisation
Some common codes:
- BS EN ISO 9606
- BS 4872
- BS EN ISO 15614 -1
- AWS D1.1/ D1.2/ D1.6
- ASME Section IX
Welding Qualification Forms
There are three fundamental forms used to track welding codes. These are:
Welding Procedure Specification (WPS)
A WPS sets out the approved procedure for a specific type of weld.
It sets a guide for effectively creating a weld that meets all applicable code requirements.
The WPS provides information that is specific to the type of welding and the type of materials, such as:
- metal grade
- filler metal classification
- amperage range
- shielding gas composition
- Preheat and interpass temperatures
It also shows the welder’s overall direction, joint design, code requirements, techniques and parameters.
Weld Procedure Qualification Record (WPQR)
The procedures for creating and testing are documented on a Weld Procedure Qualification Record or WPQR.
A PQR is a record that’s used in producing the WPS. It serves as evidence that a WPS will create an acceptable weld.
If the test results are good, the PQR is approved and used as the foundation for drafting one or more WPS.
Welder Qualification Test Certificate (WQTC)
A Welder Qualification Test Certificate shows whether a welder possesses the skill to perform the specs of the Welding Procedure.
Key Terms Summary
- WPS: A WPS is the welding procedure specification.
- WPQR: The PQR is the procedure qualification report
- WQTC: The WQTR or welder qualification test certificate describes the results of a test
- Code: A set of rules adopted by one or more governmental bodies and enforceable by law.
How To Become A Coded Welder
To become a Coded Welded, you must take a welder coding test for the code you want to earn your certification.
You can familiarise yourself with the code by obtaining the WPS, allowing you to practice that specific type of weld.
Once you successfully pass the test, which will typically include a written and a hands-on section, you will be approved to perform welding jobs that fall under that code.
What Qualifications Does A Welder Need?
Many welders have been welding for 20 years without qualifications.
But with the industry pushing towards more regulation, welders seek qualifications to confirm competence.
There are lots of ways to study and become certified to prove your competence, such as:
- Apprenticeship
- City and Guilds Level 1 Award in Introductory Welding Skills
- City and Guilds Level 2 Award in Welding Skills
- City and Guilds Level 2 Award in Welding Techniques and Skills
- City and Guilds Level 3 Diploma in Fabrication and Welding Engineering Technology
- T Level in Engineering, Manufacturing, Processing and Control
- Welder Competence Certification
- British Standard 4872 Class 2 Welder Coding Qualification
- ASME IX Class 1 Welder Coding Qualification
- ISO 9606 Class 1 Welder Coding Qualification
Most colleges will require you to have the following requirements:
- Two or more GCSEs in grades 9 to 3 (A* to D), or equivalent, for a level 2 course
- 4 or 5 GCSEs in grades 9 to 4 (A* to C), or equivalent, for a level 3 course
- 4 or 5 GCSEs at grades 9 to 4 (A* to C), or equivalent, including English and maths for a T level
A qualified welder means they have met a given standard’s requirements to become eligible to perform welding within the scope of that standard.
The Difference Between Coded Welders And Certified Welders?
The distinction between certified welders and coded welders is all down to the demonstrated ability over specific welding methods.
It is possible to be both a coded and certified welder, yet they do not mean the same thing, so it is vital to keep this in mind.
While a certified welder can produce their credentials, a coded welder has passed practical tests which indicate their skill. I.e. If they refer to a standard welding code, they are talking about a welder with a code qualification.
While these terms are represented differently, they are sometimes used interchangeably within the industry, whether rightly or wrongly.
What Is 6g Coded Welding?
6G Coded Welding refers to welding pipe in the 6g position.
The number “6” represents the position of the pipes, while the letter “G” stands for the type of weld, in this case, a groove weld.
A groove weld is a joint in two metal pipes where the space between them is filled with the welding material.
6g is a challenging welding position requiring one pipe to be positioned at a 45-degree angle to the other. It also involves accomplishing the most challenging weld in the 6G join: the overhead weld.
You can be coded in 6g using BS 4872, ASME IX or ISO 9606 standards.
As we use ISO 9606, you can read more about the standard in our post “ISO 9606: What Is It?”.
What are the different types of welding?
There are many different welding types that are available today, from high-tech processes to traditional approaches.
Here’s a look at the four most commonly used welding processes we use here at Varlowe:
TIG – Also Known as Gas Tungsten Arc Welding (GTAW). TIG leaves no splatter and minimises potential defects during the welding process. We use TIG when weld integrity is critical and requires high-quality welds.
MIG – Also known as Gas Metal Arc Welding (GMAW). MIG is the most common industrial welding process. It produces high-quality welds much quicker. It also covers a wide variety of metals and alloys.
MMA – Also known as Stick Welding or Shielded Metal Arc Welding (SMAW). MMA is a low-cost technique and is very versatile. Once mastered, the engineer can use it on various materials in almost any environment and position.
Flux-Cored Arc Welding (FCAW) – Like MIG welding, flux-cored arc welding is based on the continuous wire feed process. It typically uses an external shielding gas to protect the weld pool, but it can also be performed without making the process extremely portable and versatile.
You can find out more about Welding types on our blog post “Welding Types“.
If you want to read more about welding in general, please visit our post “What Is Welding“.
FAQ’S
What does coded mean in welding?
In welding, “coded” means a welder is certified to meet specific industry standards or codes through training and testing. This certification ensures weld quality and safety for specialised applications.
How long does it take to become a Coded Welder?
Becoming a coded welder can take several months to a few years. It depends on your starting skill level, the specific code or standard you aim to meet, and the training path you choose. Formal programs typically last a few months, but self-study may take longer. Gaining practical experience is essential for success.
What is the difference between a coded welder and a qualified welder?
The distinction between certified welders and coded welders comes down to their level of expertise in specific welding techniques. A certified welder can provide credentials, whereas a coded welder has demonstrated their skills through practical testing.
What are the duties of a coded welder?
Coded welders primarily perform welding operations, ensuring the quality and integrity of welds while following specific procedures. They also handle material preparation, maintain equipment, and document their work. Safety compliance and adherence to industry standards are paramount. Additionally, they may collaborate with teams, troubleshoot welding issues, and stay updated on welding advancements.
Coded Welders at Varlowe Industrial Services
Here at Varlowe Industrial Services, we have a team of multi-coded welders who can cover an extensive range of specifications, materials, diameters and thicknesses.
Our coded welders can work from our fully equipped mobile welding vehicles, allowing us to offer support at your site, even in remote locations, nationwide. Take a look at our mobile welding service.
Visit our Coded Welding page for more information on our Coded Welding services.
If you wish to speak to somebody, please call 01902 861042 or email info@varlowe.co.uk.
For more on the different welding types, please visit this post from Cromweld.
You can also find more information on Wikipedia.