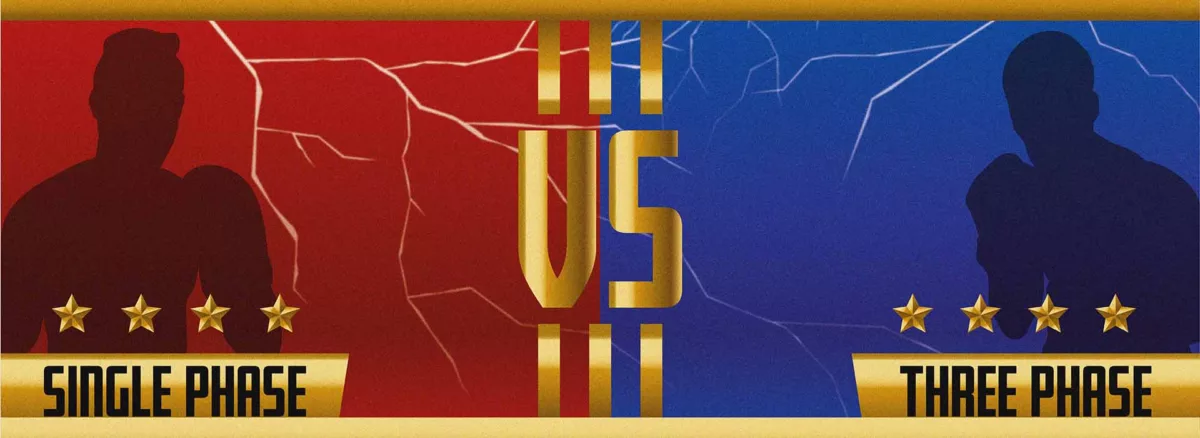
Around 90% of the electrical energy we use is from AC power.
AC stands for ‘alternating current’, which indicates the current constantly changes direction.
In the Uk, Mains electricity is about 230 volts on an AC supply.
It has a frequency of 50Hz (50 hertz), meaning it switches direction and back again 50 times a second.
AC is better for transporting electrical current over long lengths, so we use it to power our homes, offices and industrial machines.
AC Power is delivered in either a Single or Three Phase system.
What does ‘Phase’ in Electricity mean?
In electricity, the term “Phase” refers to a fundamental characteristic of alternating current (AC) that quantifies the number of electrical cycles occurring within a single second. This measurement helps us understand the frequency of AC power.
To determine the phase of an AC system, we often divide its frequency into discrete parts. Consider the following examples:
- A standard AC power system in many parts of the world operates at 60 Hz. When we divide this frequency by itself (60 ÷ 60), the result is 1. This means that within each second, there are 60 complete electrical cycles or oscillations, transitioning back and forth from positive to negative voltage (or current) and back to zero.
- Alternatively, if we consider a system with a frequency of 120 Hz, dividing 120 by 120 also yields 1. In this case, 120 electrical cycles take place within each second.
A single-phase (1-phase) has less power, requiring two wires, while a three-phase (3-phase) requires more, including three or four wires.
What is Single Phase Power Supply?
Single-phase is the most familiar system used in homes.
In power distribution, a single-phase uses the Phase and neutral wires. The phase wire carries the current load, while the neutral wire provides a path where the current returns. It is distributed in which all the supply voltages vary in unison.
It creates a single sine wave (low voltage). The standard voltage for a single-phase power starts at 230V. Also, its frequency approximates to 50Hz.
Single Phase Supply Applications
The applications of single-phase supply include the following:
- It is used to supply power for homes and non-industrial businesses.
- Can run the motors up to about five horsepower (hp).
Single Phase Advantages And Disadvantages
Advantages
The advantages of choosing a single-phase supply include the following:
- It is the standard power supply for almost all residential properties as domestic devices such as lights, coolers, heaters, fans, small air conditioners etc.
- The design and operation are often simple.
- A single-phase supply is sufficient for loads up to 2500 Watts (Depending on the region) and is the most efficient AC power supply for up to 1000 watts.
- Fast installation of the single-phase distribution system
- It does not require the balancing of the load.
- A vast collection of applications uses
Disadvantages
The disadvantages of choosing a single-phase supply include the following:
- Low efficiency
- Poor power factor. Additionally, we have to install a capacitor bank.
- Frequent power failure and requires additional inverters to maintain the power failure
- Cannot run heavy loads.
What is Three-Phase Power Supply?
Three-phase electric power is an AC Power type commonly used in industrial and business settings.
A three-phase supply is used to run the high loads, such as large induction motors, other electric motors, and other heavy loads.
A 3-phase system is a polyphase system with three power wires (or four, including an optional neutral return wire), each 120⁰ out of Phase with the other.
When a cycle of 360⁰ is completed, three phases of power peak in voltage twice.
The three-phase system can also be used as a single-phase system when using a low load by taking one phase and a neutral.
Three Phase Supply Applications
The applications of the three-phase supply include the following:
- Used in power grids, mobile towers, aircraft, shipboard, and other electronic loads larger than 1000 watts.
- Preferred power supply in industrial, manufacturing, and large businesses.
- High-density data centres.
Three Phase Advantages And Disadvantages
Advantages
The advantages of selecting a three-phase supply include the following:
- Less loss of power faults
- The efficiency of the Conductor is Greater.
- Facility to Run High Power Loads
- A three-phase power supply uses less wire than a single-phase power supply for the same power.
- To run commercial and industrial loads.
- Almost all the power is generated in three-phase power.
- The overall efficiency of the three-phase supply is better when compared to the same load on a single-phase power supply.
Disadvantages
The disadvantages of choosing a Three-Phase supply include the following:
- Cannot handle the overload, which may damage the equipment, resulting in higher costly repairs.
- Due to the high voltage, a three-phase power connection requires high insulation costs.
Single Vs Three Phase Power Supplies
Here are the essential differences between a single-phase and three-phase connection.
- In a single-phase, the flow of Electricity is through a single conductor, whereas a three-phase connection consists of three separate conductors.
- The voltage in a Single Phase may reach up to 230 Volts, while Three Phases can carry up to 415 Volts.
- Single-phase connection requires two separate wires. One represents the neutral wire, and the other represents a single phase. Three Phase requires one neutral and three-phase cables to complete the circuit.
- Single-phase connection has one phase wire, which means the complete power supply gets interrupted if anything happens to the network. However, if anything happens to a single-phase, the other phases still work in a three-phase power supply. As such, there is no power interruption.
- A three-phase supply needs fewer conductors than a single-phase power supply for the same circuit.
Uk Mains Voltage
The electrical supply we link to is delivered from a generating station or renewable power source through the National Grid.
Electricity’s voltage is reduced through sub-stations as electricity moves through the grid.
It is eventually into the three Phase and single-phase power supplies we use.
The International Electrotechnical Commission groups the voltages (in IEC 60038) into the following categories:
- Low Voltage (LV) up to 1000Vac
- Medium Voltage (MV) from 1000V to 35kVac
- High Voltage (HV) from 35 to 230kVac
- Extremely High Voltage (-) above 230kVac
In 1995, electricity supply voltages in Western Europe were harmonised to 230Vac single Phase and 400Vac three Phase.
In the UK, the standard single-phase mains power supply voltage was 240Vac. The standard three-phase mains power supply voltage was 415Vac.
Difference between Single and Three Phase Power Table
Single Phase | Three Phase |
---|---|
The flow of Electricity is through a single conductor | The flow needs three separate conductors |
Voltage may reach up to 230 Volts | Voltage can reach up to 415 Volts. |
The two wires (conductors) in a single-phase system are called Phase and Neutral. | The three wires (conductors) in a three-phase system are called phases. |
As there is only a single wire, there is only one AC Signal | All three wires carry an AC signal, and are 120° apart. |
Power delivery in a single-phase supply is inconsistent due to peaks and dips in voltage. | The power delivery in a three-phase supply is always steady due to the peaks and dips being compensated by each other. |
Less efficient than a three-phase supply for the same power delivery | More efficient as it can deliver three times the power than a single-phase power supply with just one additional wire |
Served to residential and domestic needs | Served to large commercial centres and industries. |
As there is only one phase, chance of fault is higher | Even if there is a fault in one or two phases, the remaining Phases will continue to deliver power |
Electrical Services At Varlowe
Varlowe’s electrical engineers are well experienced in working with both single and three phase systems.
Our Electrical department delivers nationwide support for clients in both commercial and industrial sectors.
For more information, please visit our electrical service page, or call us on 01902 861042.